Versorgung mit
flüssigen Materialien
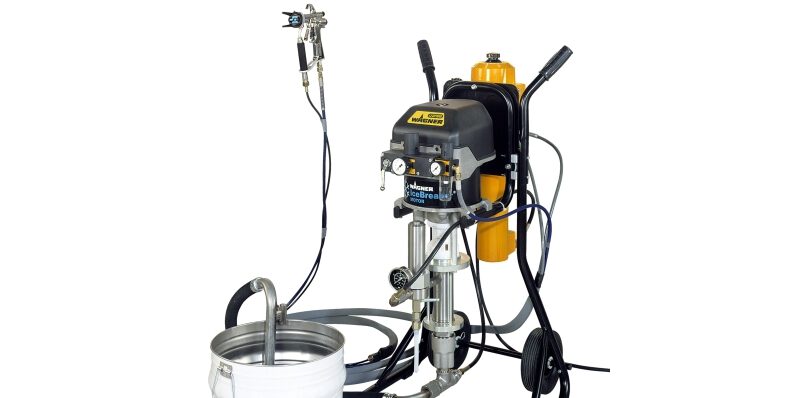
Versorgung mit flüssigen Materialien / Versorgungstechnologien für flüssigen Materialien wie z. B. flüssige Farben. Mittels der Hochdruck-Kolbenpump wird das zu verarbeitende Material von dem Materialvorratsbehälter über die Pumpe in einen Hochdruckschlauch an die Lackierpistole gefördert. Dabei wird ein Materialdruck aufgebaut, mit welchem das Material durch die Düse an der Pistole gepresst und in kleinste Tröpfchen zerstäubt wird. Diese benetzen die Oberfläche des Werkstückes und vereinen sich zu einem geschlossenen Film. Das Förderprinzip dabei ist die Verdrängung, da der Hubkolben das zu verarbeitende Material nach dem Ansaugen in den Schlauch schiebt. Damit gehört die Kolbenpumpe zu den Verdrängerpumpen.
Erfahren Sie hier mehr
Versorgung mit flüssigen Materialien / Versorgungstechnologien für flüssigen Materialien wie z. B. flüssige Farben.
Mittels der Hochdruck-Kolbenpump wird das zu verarbeitende Material von dem Materialvorratsbehälter über die Pumpe in einen Hochdruckschlauch an die Lackierpistole gefördert. Dabei wird ein Materialdruck aufgebaut, mit welchem das Material durch die Düse an der Pistole gepresst und in kleinste Tröpfchen zerstäubt wird. Diese benetzen die Oberfläche des Werkstückes und vereinen sich zu einem geschlossenen Film. Das Förderprinzip dabei ist die Verdrängung, da der Hubkolben das zu verarbeitende Material nach dem Ansaugen in den Schlauch schiebt. Damit gehört die Kolbenpumpe zu den Verdrängerpumpen.
Aufbau: Die Kolbenpumpe besteht aus einem Zylinder, in dem sich ein Kolben befindet. Der Zylinder hat einen Zulauf mit Einlassventil (Ansaugseite) und einen Ablauf mit Auslassventil (Druckseite) damit ist sichergestellt, dass das Fördermedium nur in eine Richtung bewegt wird.
Wenn sich der Kolben vom Zugang durch die Hubbewegung entfernt, entsteht ein Vakuum bzw. ein Sog. Dadurch wird automatisch das Ventil geöffnet und das Material wird in den Zylinderraum gesogen. Wird der Kolben nun durch die Kolbenstange in die entgegengesetzte Richtung geschoben, also zum Auslass hin, wird das Verschlusselement des Auslassventils durch den Druck angehoben und das Fördermedium in den Schlauch gepresst.
Dadurch, dass nun durch die folgenden Kolbenhübe immer mehr Material angesaugt und schließlich in den Schlauch gedrückt wird, wird es auch innerhalb des Schlauches immer weiter zur Pistole gedrängt, bis es schließlich aus der Düse herausgepresst und zerteilt wird.
Eine Kolbenpumpe ist kein Dauerläufer. Sie springt nur an, wenn der Druck unter eine bestimmte Grenze fällt, wie beim Auftragen des Materials. Dann wird der erforderliche Materialdruck wieder aufgebaut und stoppt wieder, wenn der von dem Bediener vorgegebene Förderdruck erreicht ist.
Kolbenpumpen gibt in drei Antriebssystemen: elektrisch, mit Benzin betrieben oder pneumatisch.
2-Kugel-Technologie für die Versorgung mit flüssigen Materialien
In einer doppeltwirkenden Kolbenpumpe (Kugel u. Sitz für das Ansaugen und Kugel u. Sitz für die Versorgung) wird, wenn der Kolben nach unten fährt, dass Saugventil den Sitz verschließen und das viskose Material wird durch die Kolbenstange aus dem „Materialkammer 2“ verdrängt.
Umgekehrt verhält es sich, wenn der Kolben dann nach oben fährt, öffnet sich das Saugventil und das Material wird in die „Materialkammer 2“ gesaugt. Das Kolbenventil (kleine Kugel) schließt dabei und das Material wird aus der Materialkammer 1 angesaugt.
Einsatzgebiet: unterschiedliche Airless Applikationen wie z. B. Möbel und Holzverarbeitung, Metallbearbeitung, Bau- und Landmaschinen Beschichtung, Werkzeugmaschinen, Container, Transportmaschinen.
Zahnrad-Technologie
Ein von einem Motor angetriebenes Antriebsrad dreht ein Laufrad in die entgegengesetzte Richtung. Durch das Drehen der Zahnräder wird die Flüssigkeit zwischen der Gehäusebohrung und der Außenseite der Zahnräder von der Einlassseite der Pumpe zur Auslassseite befördert.
Dabei ist zu beachten, dass sich die gepumpte Flüssigkeit um die Zahnräder herum und nicht zwischen den Zahnrädern bewegt. Die sich drehenden Zahnräder fördern ständig neue Flüssigkeit von der Saugseite (Einlassseite) zur Druckseite (Auslassseite) der Pumpe.
Membran-Technologie
Doppelt-Membranpumpen / Verdrängerpumpen sind pneumatische Pumpen (Druckluft als Antrieb) zur Erzeugung von niedrigen Förderdrücken. Zum Pumpen der Flüssigkeit wird eine Hubbewegung einer Teflonmembran mit verschiedenen Ventilen (Rückschlagventile, Drosselventile, Klappenventile oder eine andere Ausführung von Absperrventilen) auf beiden Seiten der Membran verwendet. Diese Hubbewegung drückt Flüssigkeit aus einer der Kammern in den Auslassverteiler, während die andere Materialkammer durch den Einlassverteiler gefüllt wird. Bei der nächsten Hubbewegung wird die zuvor gefüllte Kammer entleert und die erste Kammer gefüllt. Die schnellen Hubbewegungen sorgen dafür, dass die Pulsation geringgehalten wird.
Einsatzgebiet: Dieser Pumpentyp eignet sich für Grundierungen, Decklacke und Trennmittel.
Quatro-Technologie
Bei der Quatro Technologie wird mittels eines Kolbens, der über zwei Materialkammern mit exakt dem gleichen Volumen läuft, durch Auf- und Abwärtsbewegung eine hohe Strömungsgeschwindigkeit ohne Pulsation erzeugt. Diese Pumpen erfüllen die hohen Leistungs- und Lebensdaueranforderungen der Automobilindustrie. Sie werden als Nieder- oder Hochdruckpumpen gebaut.
Umschaltmotor- Technologie
Diese Technik wird bei Druckluftmotoren eingesetzt. Der Umschaltmotor hat 2 Kammern, in denen ein Pumpenkolben auf und ab bewegt wird. Während die eine Kammer geleert wird, füllt sich die anderen und umgekehrt. Eignet sich für hohe Ausbringmengen, dabei wird der Pulsationseffekt weitestgehend vermieden.
Dachmanschetten-Dichtung an Pumpen für hochviskose Materialien
Diese sind Pumpen Systeme, die mit Mehrschichtdichtungen ausgerüstet sind. Die Materialien der Mehrschichtdichtungen richtet sich nach den eingesetzten zu förderndem Material z. B. Leder, PE, PU, PTFE-Graphit, PTFE und sind daher sehr geeignet für abrasive Materialien. Sie zeichnen sich durch eine lange Lebensdauer aus, dass die Dichtungen wiederholt nachgezogen werden können.