Klebepistolen
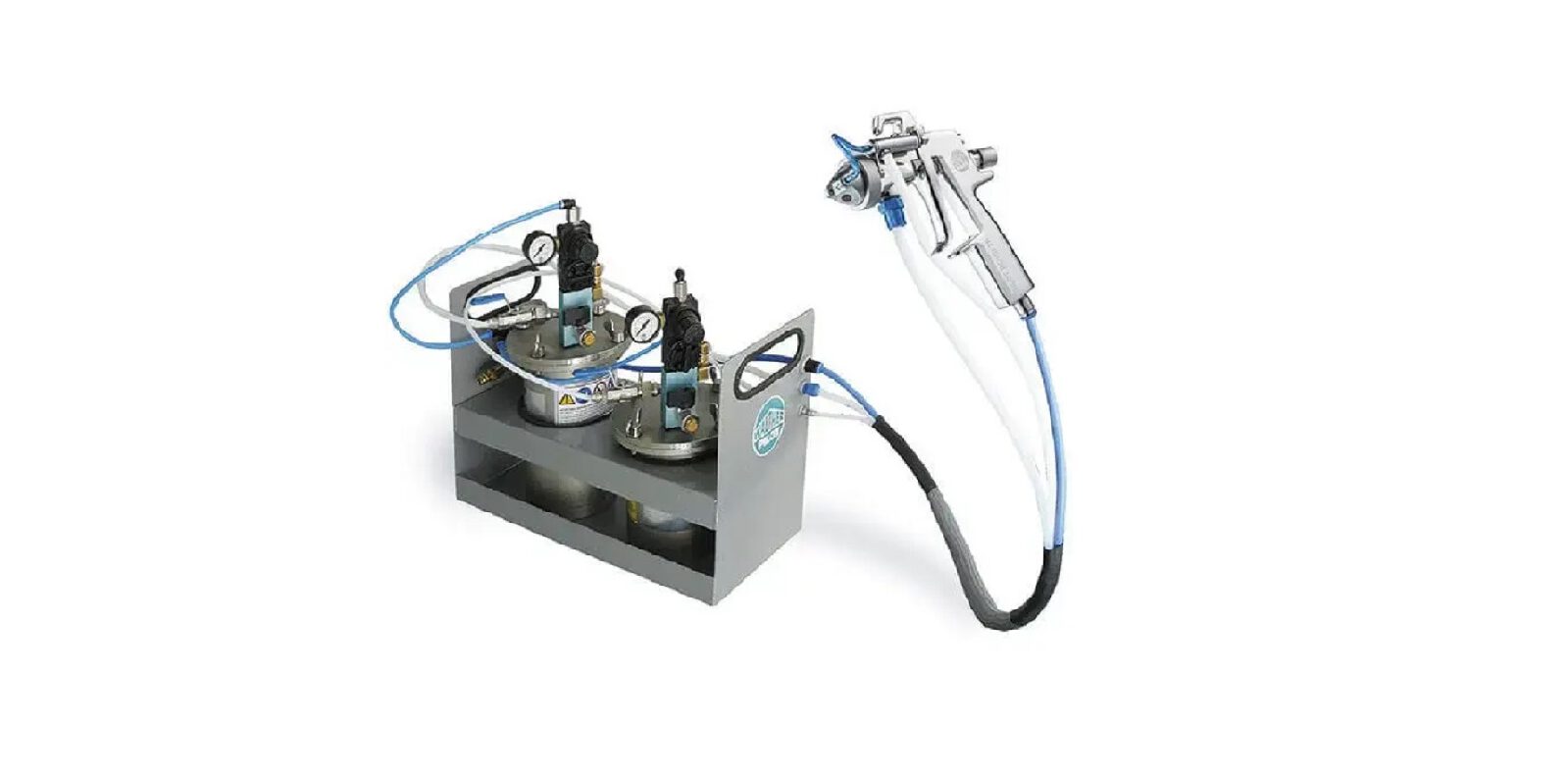
Verarbeitung von Klebstoff: Klebstoff ist eine Substanz, die auf eine oder beide Oberflächen von Werkstoffen aufgebracht wird, um diese durch Oberflächenhaftung (Adhäsion) und seine innere Festigkeit (Kohäsion) zu verbinden. Kleber härten durch physikalische Trocknung oder chemische Reaktion aus. Klebepistolen: Unterscheiden sich vorwiegend darin, dass die Nadelgeometrie bei einer Klebstoffpistole eine andere ist als die einer Farbspritzpistole. Die Nadel einer Klebepistole schließt die Materialdüse von hinten und nicht wie bei einer Farbspritzpistole von innen. Daher hat die Klebepistole eine längere Einsatzdauer und ist wartungsfreundlicher beim Einsatz. Materialdüse und Nadel sind aufeinander abgestimmt und sollten immer paarig ausgetauscht werden. Grundlagen zur Verarbeitung von Klebstoffen: Wasserbasierende (Dispersionsbasierende) Klebstoffe: Empfohle
Erfahren Sie hier mehr
Klebstoff:
Substanz, die auf eine oder beide Oberflächen von Werkstoffen aufgebracht wird, um diese durch Oberflächenhaftung (Adhäsion) und seine innere Festigkeit (Kohäsion) zu verbinden. Kleber härten durch physikalische Trocknung oder chemische Reaktion aus.
Klebepistolen: Unterscheiden sich vorwiegend darin, dass die Nadelgeometrie bei einer Klebstoffpistole eine andere ist als die einer Farbspritzpistole. Die Nadel einer Klebepistole schließt die Materialdüse von hinten und nicht wie bei einer Farbspritzpistole von innen. Daher hat die Klebepistole eine längere Einsatzdauer und ist wartungsfreundlicher beim Einsatz.
Materialdüse und Nadel sind aufeinander abgestimmt und sollten immer paarig ausgetauscht werden.
Grundlagen zur Verarbeitung von Klebstoffen:
- Wasserbasierende (Dispersionsbasierende) Klebstoffe: Empfohlen mit Niederdruckpistolen (HVLP) um Overspray zu reduzieren und zur Vermeidung von lungengängigen Tröpfchen.
- Lösemittelbasiert: Empfohlen konventionelle Zerstäuber mit ggf. Drehstrahldüse, da eine höhere Energie für die Zerstäubung erforderlich ist.
- Scherenempfindliche Medien: Klebstoff darf keinem Materialdruck ausgesetzt werden, daher vorzugsweise einen Druckbehälter anstelle einer Pumpe zur Materialförderung einsetzten. Verarbeitung mit Niederdruckpistolen (HVLP) und bei Automatisierung ggf. mit Membran-Nadeldichtung.
Anwendungsgebiete:
Klebstoff-Lösemittelbasiert: Matratze, Sofas / Schäumen, Textil, Möbel, Schuhe, Leder
Klebstoff-Wasserbasiert: Matratze, Sofas / Schäumen, Automotiv Interieur, Textil, Möbel, Schuhe, Leder
- 1-Komponentig: Matratze, Sofas / Schäumen, Automotiv Interieur, Textil, Möbel, Schuhe, Leder
- 2-Komponentig: Matratze, Sofas / Schäumen, Automotiv Interieur, Textil, Möbel, Leder